Sinker EDM Machining is Our Specialty
Sinker EDM work is tricky, especially in production. It takes a skilled machinist to design a sinker EDM process that is cost-effective, precise, and repeatable.
That’s why world-class manufacturers depend on Custom EDM to set them up for success.
Sinker EDM Services
When you need to cut large, complex shapes with difficult features on parts and components that have already been carefully machined and processed–making them worth hundreds or thousands of dollars–Sinker EDM may be the way to go. With a traditional mill or lathe, your cutting tool places a large amount of force on your workpiece, putting it at risk. But with EDM, the “cutting tool” is an electric current that gently burns away the material without ever contacting the workpiece. And with Sinker EDM (also called Conventional EDM, Die Sinking EDM, Spark Erosion Machining, Plunge EDM, or Ram EDM), we can make the electrode (the cutting tool) in virtually any shape–removing many typical design restrictions. Achieving unparalleled accuracy and reliability, this no-contact machining process is ideal for secondary operations.
Using our vast library of EDM technologies, we can provide you with the best surface finishes in a wide range of materials. Sinker EDM services are offered by Custom EDM from prototype through production. If you have a difficult part that you’re having trouble machining, our expert staff will help you find the best solution.
What’s The Difference Between Sinker EDM & Wire EDM?
Wire EDM also uses an electrode carrying an electric current that burns away the material without ever touching the workpiece. However, a wire electrode needs to be tightly held on both ends and so it can cut through the material like a cheese slicer. With Sinker EDM, the electrode is a solid shape that “sinks” into the material, so it does not need to cut all the way through. This makes Sinker EDM the ideal solution for a wide range of applications, such as blind cavities or keyways, thin walls, or cross-sections. Injection molding and stamping die components can benefit from Sinker EDM's versatility as can certain complex production components.
Competitive Electrical Discharge Machining Solutions
Sinker EDM is where we really shine. Over the past 50 years, we have completed thousands of Sinker EDM projects. What differentiates Custom EDM manufacturing services from the competition is our ability to not only hold close tolerances but to do so while offering globally competitive pricing and lead times. Custom EDM specializes in providing Sinker EDM services. We have the industry experience to know what works and what doesn’t, so you can ensure that your project will be a success.
Contact us with your request for pricing on your Die Sinking EDM project today!
Sinker EDM Capabilities
With the versatility and efficiency of our Sinker EDM machining capabilities, we can instantly multiply your productivity and save you time and money. From in-house design and machining of electrodes and fixturing from a wide variety of conductive materials to state-of-the-art Sodick Sinker EDM machines and decades of expertise and experience with one-off parts to high-volume production, our customers trust us to get the job done right the first time and every time after that.
By fixturing and burning (cutting) multiple parts at once with multi-up electrodes, we can deliver high volumes of precise, repeatable, quality-conforming components fast. With tolerances ranging from standard (0.0050″ to 0.0010″) to high precision (as tight as 0.0002″ or 5 microns), our expert staff can cut complex shapes with extreme consistency using our 4-Axis CNC Sinker EDM machines.
We’ve even developed our own proprietary process for die sinking in deionized water–or as we call it, CleanSinker EDM.
Sinker EDM Manufacturing Specifics:
Advanced 4-Axis CNC Sinker EDMs built for efficient 24/7 operation
Any sinker electrode material including copper, graphite, and copper tungsten
We can machine workpieces up to 22″ thick with Sinker EDM
Simultaneous machining of multiple parts using multi-up Sinker EDM techniques
Standard machining tolerances of 0.0050″ to 0.0010″ and high precision tolerances as tight as 0.0002″ (5 micron)
Surface Finishes down to 12 RMS
Sinker EDM prototype development through contract manufacturing
Sinker EDM Materials
Custom EDM strives to meet your specific needs. Through strategic sourcing partnerships with a vast array of qualified material suppliers nationwide, we can manufacture your components from the exact materials that you require. Strict quality standards are met by all vendors and material suppliers to Custom EDM to ensure that the components we produce can meet the highest standards commonly required by the Aerospace, Automotive, Communications, Defense, Medical, and Scientific industries.
Sinker EDM is the ideal solution for large, high-value components and for extremely thin and fragile materials. Materials like hardened tool steel and tungsten carbide are no match for the Sinker EDM erosion process because the electrode never actually makes contact with the workpiece.
Custom EDM has completed thousands of Sinker EDM projects using a diverse set of materials including those listed below.
Don’t see your specific material on the list? Contact us to determine if it can be cut using CNC Electrical Discharge Machining and how Custom EDM can source that material for you.
Common Sinker EDM Applications
When components require deep pockets, blind cuts, and/or screw threads, Sinker EDM machining could be an ideal solution. Sinker EDM is also well suited for parts requiring tight tolerances, minimal material stress and thermal heating, and fine surface finishes. Through multi-up Sinker EDM processing, the quantities of parts being burnt simultaneously can easily be scaled up to meet the high volumes required by some of our largest customers.
In over 50 years serving vital industries like Aerospace, Automotive, Communications, Defense, Medical, and Scientific, Custom EDM has seen it all. No project is too big or part too complex or tolerance too tight for our shop which makes us the go-to partner for OEMs and subcontractors nationwide. To learn more about how Custom EDM can help you, reach out to us for pricing.
Aluminum
Brass
Copper
Exotic Metals
Molybdenum
Titanium
Tungsten
Carbide
Tool Steels
Inconel
Hastalloy
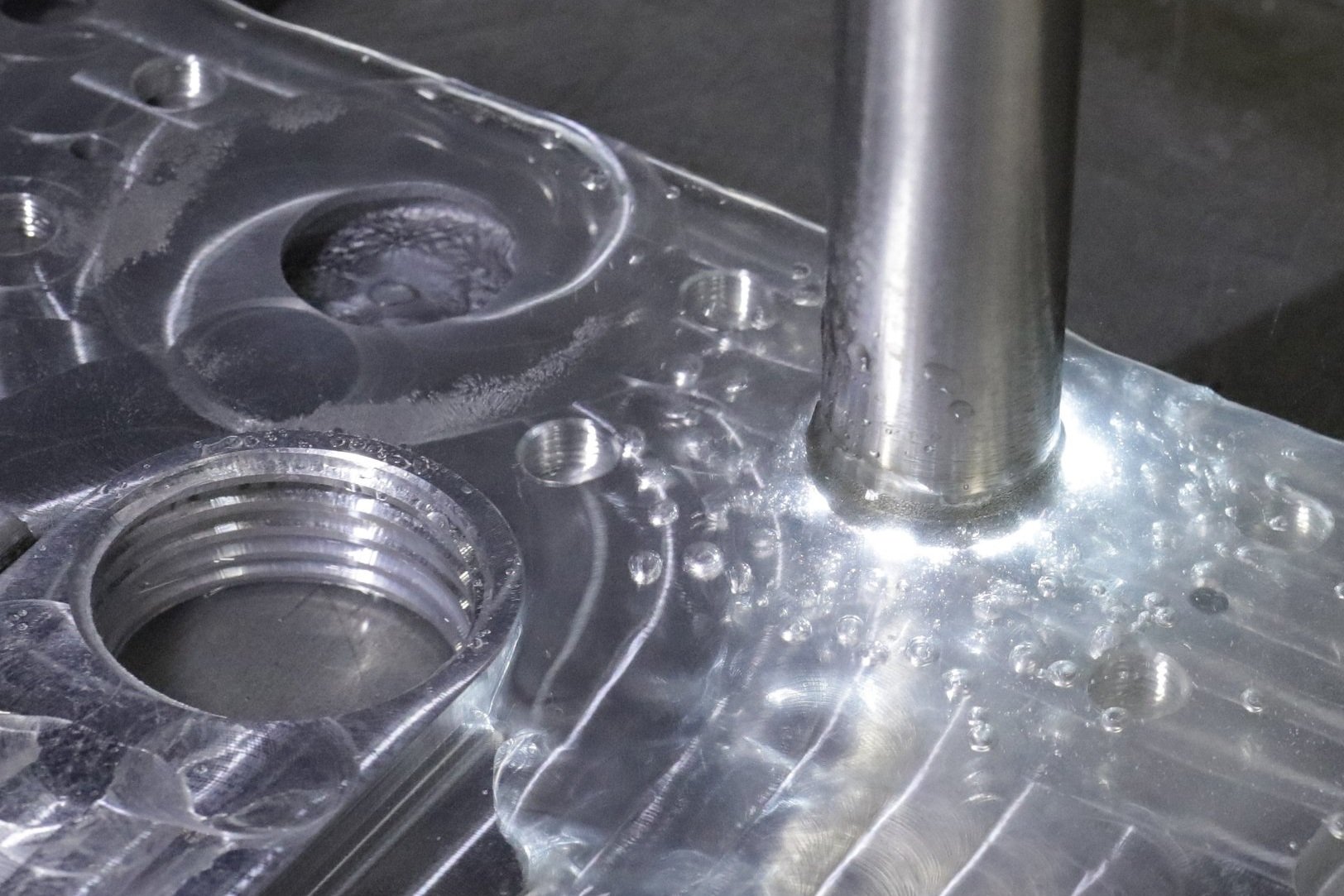