Wire EDM Machining
When you’re under the wire to source parts with complex geometries, tight tolerances, and small features out of difficult (or impossible)-to-machine materials, Custom EDM has you covered.
Many shops have wire EDM machines, but few have the expertise and range of capabilities we do.
Wire EDM Machining Services
For over 50 years, Custom EDM has specialized in EDM (electric discharge machining) processes including Wire EDM. That expertise has made us the go-to EDM shop in Silicon Valley for top Aerospace, Automotive, Communications, Defense, Medical, and Scientific device manufacturers. Stocked with the latest state-of-the-art wire EDM machines, we are able to manufacture precise, repeatable, high-quality parts and components from any conductive material. Wire EDM machining gives us the ability to produce complex shapes with small features and tight tolerances in materials that are often impossible using traditional CNC machining methods. Our newest Wire EDM machine can deliver the most precise cuts possible because, in addition to burning the material with an electric current, the wire rotates.
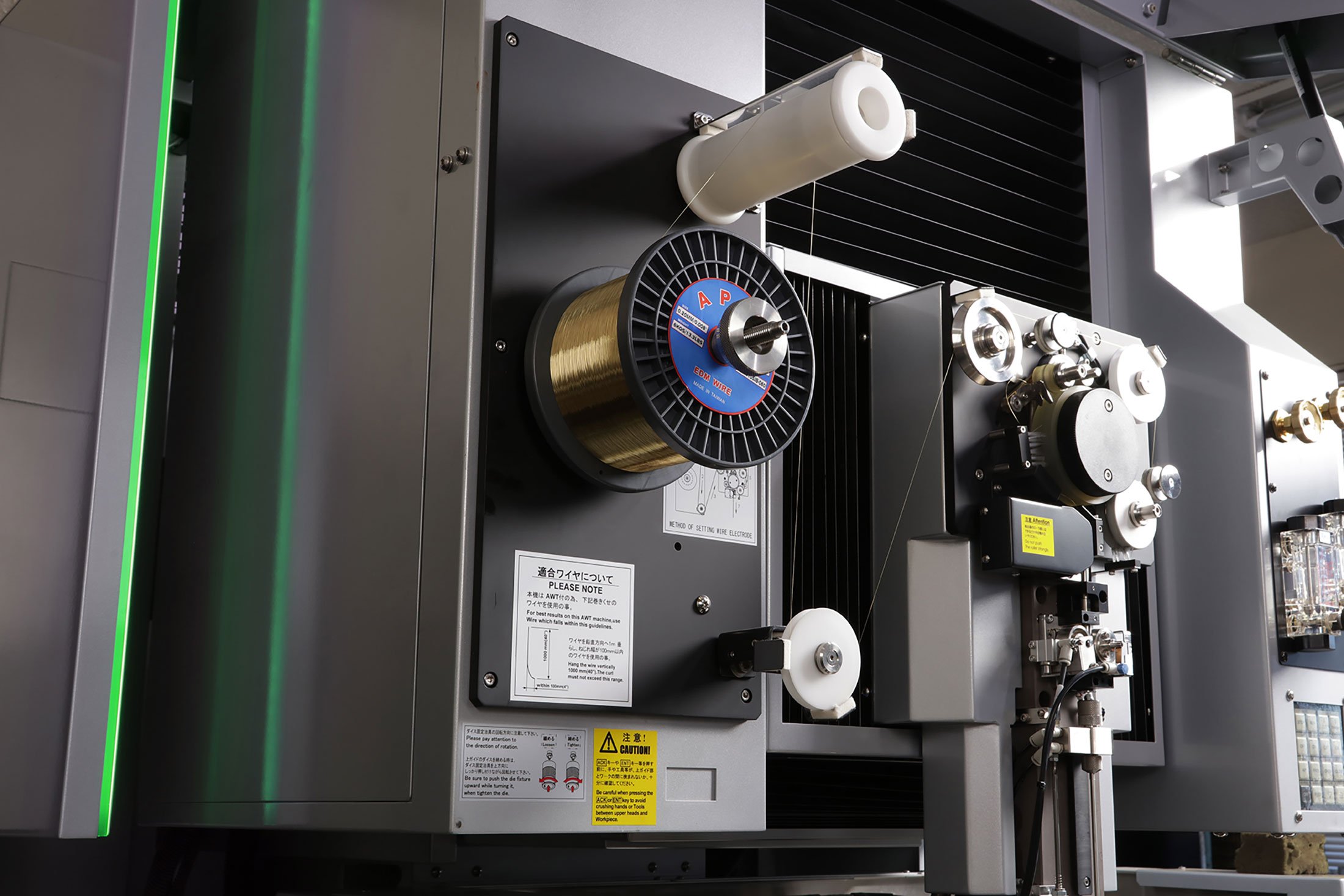
Wire EDM is even more precise when the wire rotates…
The latest in wire tech–just for you.
What is Wire EDM?
With Wire EDM (Electrical Discharge Machining), we feed a single strand of thin wire into a small hole that we punch into the workpiece and apply an electric current under high-pressure deionized water that burns a precise cut. Similar to a band saw blade, many miles of wire electrodes are continuously fed between two guide rollers that are driven by CNC machine control.
The EDM process removes conductive materials from the workpiece by eroding them away with electric current, leaving behind a smooth, uniform surface that does not need to be polished or finished. Because the cutting tool (the wire) does not actually touch the workpiece, Wire EDM is ideal for delicate materials and intricate shapes.
Deionized water uniformly carries the spark from the wire to the workpeice and keeps it cool while flushing away metal particles removed during the process.
Wire Edm Capabilities
We offer standard tolerance of (0.0010″ to 0.0005″), as well as high precision tolerances as tight as 0.0001″ (2 microns) for an array of industries and applications. Our 5-Axis CNC Wire EDM machines offer superior cutting consistency and have the capacity to run multiple wire electrode sizes, .0040-.0120 in diameter. Wire EDM cutting can produce extreme machining efficiency when multiple parts are stacked and cut simultaneously. Depending on the part geometry, multiple identical components can be produced in the same machining cycle using stacked sheets of material. This instantly multiplies productivity and saves time and money for our customers.
Decades of EDM experience paired with the latest tech allow us to deliver repeatable quality parts and components made of any conductive material. As our diverse customer base continues to evolve, we are continuously upgrading our Wire EDM machining capabilities through our technology partners.
Advanced 5-Axis CNC Wire EDMs built for efficient 24/7 operation
Multiple wire electrode sizes from 0.0120″ down to as small as .0040 in diameter
Multiple wire electrode materials are used like brass, copper and coated wires.
Extremely consistent cut quality due to the wire electrode being cycled between spools during the cutting process
Workpieces up to 13.75″ thick are easily machined using Wire EDM
Simultaneous machining of multiple parts using stacked Wire EDM techniques
Standard machining tolerances of 0.0010″ to 0.0005″ and high precision tolerances as tight as 0.0001″ (2µm micron)
Surface Finishes down to 8Ra µin (micro inch) eliminate finishing and require no additional polishing
Small quantities of 1-50+ pieces with quick turnarounds
Contract Manufacturing of full production quantities of thousands of pieces
Wire EDM Manufacturing Specifics:
Wire EDM Materials
Our goal at Custom EDM is to meet your specific needs. By partnering with a vast array of qualified material suppliers nationwide, we are able to manufacture your components from exactly what you need. Custom EDM maintains strict quality standards with all vendors and material suppliers, ensuring our products comply with the most stringent requirements for Aerospace, Automotive, Communications, Defense, Medical, and Scientific applications.
Wire EDM is compatible with a wide range of metals that conventional machining, such as milling and turning, cannot. Hardened materials such as tungsten carbide are no match for wire EDM erosion. Softer materials like copper are gently shaped by the Wire EDM electrodes. The wire never actually makes contact with the workpiece, thus preventing damage to extremely thin materials.
We have completed wire EDM projects using a variety of materials, including those listed below. Don’t see your specific material on the list? Find out how CNC Electrical Discharge Machining can cut that material and how Custom EDM can source it, by contacting us.
Aluminum
Brass
Copper
Exotic Metals
Molybdenum
Titanium
Tungsten
Tool Steels
Common Wire EDM Applications
Wire EDM machining is recommended when components require cuts through the entire thickness of the raw material. Wire EDM is well suited for parts requiring intricate tolerances, limited material stress, and superior surface finishes. It can also be a high-volume alternative to die stamping when the material is brittle or delicate. Through Wire EDM processing, the quantities of parts being cut simultaneously can be easily scaled up to meet the high volumes required by some of our largest customers.
No project is too large, parts too complex, or tolerance too tight for Custom EDM which makes us the preferred partner for OEM manufacturers nationwide. To learn more about how Custom EDM can help you with your EDM Metal Cutting project, contact us for pricing.
Sample Wire EDM Applications
Interconnect Components
Fiber Optic Components
Medical Components
Research & Development
Aerospace Components
Defense Components
Research and Scientific Labs
Ready to work with an EDM machine shop that gets it?
Machine shops bring us their most precious parts for EDM cutting and drilling because they know we’ll handle them with the utmost care and make those final cuts with the highest level of precision.
World-class corporations bring us their most unique design challenges because they know we can develop and execute an innovative solution–and often reduce their production costs.